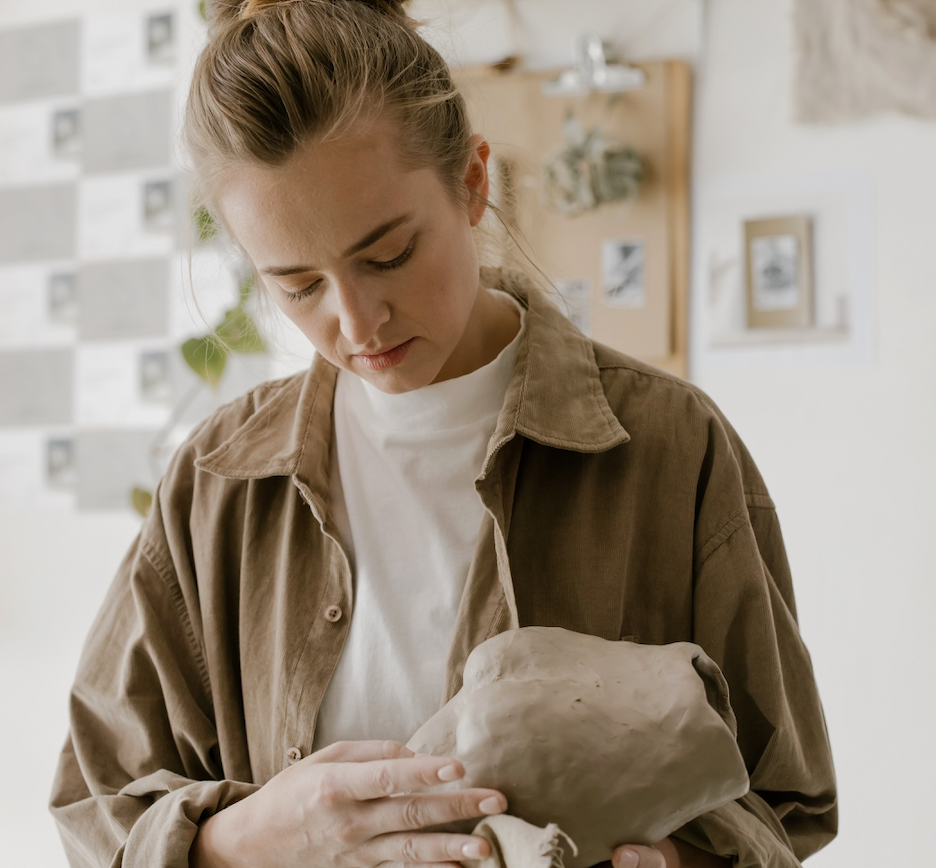
How do you make a Bole ceramic bowl?
What is behind each product?
Today we want to talk about our ceramic feeding bowls made in our workshop in Portugal. Laura and Anna are in charge of providing the knowledge and hands to create these pieces made by hand one by one. When we learned about its history and how each product is made, the whole team fell in love with the Bole feeder.
This is the beautiful part of starting a project like this, that artisans open the doors of their house for you and give you little bits of knowledge that have an incalculable value.
We realized the work involved in making a product like this and the value we must give it. Laura showed us her hands, which are like a perfect tool that, when in contact with the clay, is capable of understanding the humidity and the state of the material to calibrate the tempos in which she makes each elaboration with her wheel.
The process to make a handmade ceramic bowl.
1: We start:
We start by preparing the perfect base in clay and water and letting the mixture rest on top of the lathe. It is important to select the right clay for your project. Pottery clay falls into two categories: fine-grained clay and coarse-grained clay. Fine-grained clay is used to make fine, delicate objects, while coarse-grained clay is used to make sturdier objects.
2. Form the piece:
At this point, a dialogue begins between Laura's hands and the clay that is very complex to explain. But after a continuous massage in the style of the movie " Ghost " we end up with the result of the shape of our bowl. Subsequently, we let it dry to let the moisture out of the mixture, and then comes the baking process. A kind of special chamber where they put all the pieces that they have been making by hand and thus, when firing the product, ensure its rigidity and shape.
3. Straightening:
Once the part has been formed, it is important to smooth the surface to remove any irregularities and leave it with a smooth surface.
Drying: The drying time varies depending on the size and thickness of the piece. It is recommended to leave the piece in a dry and ventilated place until it is completely dry before continuing with the next step.
4. Baking:
Once the piece is completely dry, it must be fired in a kiln specially designed for ceramics at a specific temperature. This process is known as firing and is important to strengthen the ceramic and give it strength.
5. Painting and finishing:
Once the piece is fired, it can be painted and finished if necessary.
Second firing: A second firing is carried out so that the pigment and glazes are fixed to the piece, and thus the desired final finish is obtained.
After getting to know the whole process and the two of them, we are all grateful to be able to have this experience and we have all become a bit of a ceramic freak .
If you want to enjoy any of the ceramic products made by this workshop, do not hesitate to take a look at the web. We hope we have explained well the importance of craftsmanship in the products and in our day and that your activist pets enjoy it a lot.
Leave a comment
This site is protected by hCaptcha and the hCaptcha Privacy Policy and Terms of Service apply.